.jpeg)
Process Manufacturing Software: The Ultimate Guide to Cost Reduction and Efficiency
Process Manufacturing Software: The Ultimate Guide to Cost Reduction and Efficiency
Process manufacturing is a complex and competitive industry, where success is often determined by the ability to minimize costs and optimize efficiency. To survive, businesses must be agile and innovative to stay ahead of the competition. One of the most effective ways to achieve this is through the implementation of Process Manufacturing Software. This comprehensive guide will delve into the benefits of using such software, key features to look for, and how to choose the right solution for your organization.
Benefits of Process Manufacturing Software
Reduction in Frequency of Stock-Outs
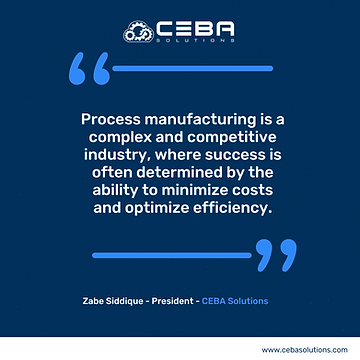
A well-designed Process Manufacturing Software can significantly reduce stock-outs and lower carrying costs. By providing real-time visibility into inventory levels and automating replenishment processes, businesses can avoid costly stock shortages and minimize the capital tied up in excess inventory.
Improved Demand Forecasting
Improved demand forecasting accuracy is another significant benefit of Process Manufacturing Software. By utilizing advanced algorithms and historical data, these systems can more accurately predict future demand, enabling better resource allocation and minimizing the risk of overproduction.
Optimized Production Schedules
Optimized production schedules and enhanced capacity planning capabilities are essential for process manufacturers. Process Manufacturing Software allows organizations to manage their production schedules effectively, taking into account factors such as machine availability, labour constraints, and material lead times, resulting in optimized production processes and improved overall efficiency.
Shorter Lead Times
Shortening lead times and responding quickly to market changes are vital for staying competitive in the process manufacturing industry. Process Manufacturing Software can streamline the entire production process, from order placement to delivery, significantly reducing lead times and enabling faster reactions to fluctuations in demand.
Simplify Purchasing Processes
Process Manufacturing Software simplifies the purchasing process and reduces waste by streamlining Material Requirements Planning (MRP). By automatically generating purchase orders based on current inventory levels and production requirements, these systems ensure that the right materials are available at the right time, preventing costly delays and excess inventory.
Improved Efficiency on the Shop Floor
Improved overall efficiency and enhanced decision-making capabilities are also notable benefits of Process Manufacturing Software. By providing real-time visibility into production processes and integrating data from multiple sources, these systems enable businesses to make more informed decisions, resulting in better resource utilization and increased profitability.
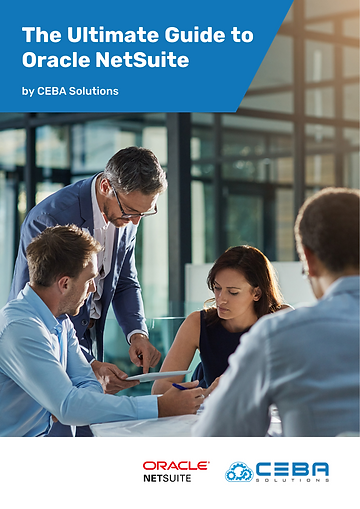
Download the Ultimate Guide to Oracle NetSuite
Learn why NetSuite is the #1 Cloud ERP for Small and Mid Size Businesses Focused on Unlocking Growth. Download the Guide
Key Features of Process Manufacturing Software
Inventory Management
Real-time tracking of inventory levels and automated replenishment are essential features of Process Manufacturing Software. By providing a comprehensive view of material availability and usage, these systems enable organizations to optimize their inventory management processes and minimize the risk of stockouts or overstocking.
Work Orders
Digital documentation and seamless communication are crucial aspects of effective work order management. Process Manufacturing Software allows businesses to create, manage, and track work orders digitally, eliminating the need for paper records and ensuring that all team members have access to the most up-to-date information.
Quality Control and Compliance
Process Manufacturing Software can help organizations maintain high-quality standards and adhere to industry-specific regulatory requirements. These systems provide tools for tracking and documenting quality metrics, automating quality control processes, and generating reports necessary for compliance. As a result, manufacturers can ensure product consistency, minimize the risk of recalls, and maintain a strong reputation in the market.
Production Planning and Scheduling
Efficient production planning and scheduling are critical to optimizing the use of resources and minimizing downtime. Process Manufacturing Software offers advanced features that enable organizations to create and manage production schedules, taking into account factors such as machine availability, material lead times, and labour constraints. This allows for better utilization of production resources and reduced idle time, leading to increased operational efficiency.
Analytics and Reporting
Analytics and reporting capabilities are crucial for making data-driven decisions and identifying areas for improvement. Process Manufacturing Software typically includes robust reporting tools that enable organizations to generate customized reports and visualize data in a user-friendly format. This provides valuable insights into production trends, equipment performance, inventory levels, and more, allowing management to make informed decisions and drive continuous improvement efforts.
Choosing the Right Process Manufacturing Software
Choosing the Right Process Manufacturing Software: A Step-by-Step Guide
Step 1: Assess Your Needs and Requirements
Before you begin evaluating different Process Manufacturing Software options, it's essential to have a clear understanding of your organization's unique needs and requirements. Consider the following factors:
- The size and scale of your operation
- The complexity of your production processes and formulations
- Regulatory compliance requirements specific to your industry
- Your budget and expected return on investment
- Integration needs with existing systems (e.g., ERP, CRM)
Step 2: Research and Evaluate Options
Once you have a clear understanding of your organization's needs, research and evaluate the available Process Manufacturing Software options in the market. Consider the following aspects when evaluating each option:
- Features and functionality: Ensure the software provides the necessary tools and features to address your specific challenges and requirements.
- User reviews and testimonials: Read user reviews and testimonials to gain insights into the software's performance, user experience, and potential issues.
- Vendor reputation and experience: Choose a software provider with a strong track record and experience in the process manufacturing industry.
- Pricing and licensing options: Compare the pricing and licensing options of various software solutions to find one that fits your budget and offers flexibility for future growth.
- Customer support and training resources: Opt for a software provider that offers comprehensive customer support and training resources to ensure a smooth implementation and ongoing success.
Step 3: Request a Demo or Trial
Once you have narrowed down your options, request a demo or trial of the software to gain hands-on experience and evaluate the solution's suitability for your organization. During the demo or trial, pay close attention to:
- Ease of use and user interface
- Customization and scalability options
- Integration capabilities with your existing systems
- Responsiveness and quality of customer support
Step 4: Make a Decision and Implement the Solution
After thoroughly evaluating your options and identifying the best Process Manufacturing Software for your organization, make a decision and proceed with the implementation process. Work closely with your implementation partner to ensure a seamless implementation, including:
- Data migration from your existing systems
- Integration with other enterprise applications
- Customization and configuration to suit your specific needs
- Training for your team to ensure effective adoption and utilization of the software
Step 5: Continuously Monitor and Optimize
Once the Process Manufacturing Software is implemented, continuously monitor its performance and gather feedback from your team. This will help you identify any areas for improvement, optimize the system to better meet your needs, and ensure you're maximizing the benefits provided by the software solution.
By following these steps, you can confidently choose the right Process Manufacturing Software for your organization, ensuring a successful implementation and ongoing improvements in your production efficiency, cost reduction, and overall competitiveness.
Conclusion
Investing in Process Manufacturing Software can have a transformative impact on your organization's cost reduction and production efficiency. By streamlining inventory control, improving demand forecasting, enhancing capacity planning, and optimizing lead time management, these systems can deliver significant benefits to your bottom line. In addition, the right software solution can address critical manufacturing challenges, ensuring regulatory compliance, seamless integration with existing systems, and customizable features to meet your unique needs.
As you embark on the journey of selecting and implementing Process Manufacturing Software, take the time to thoroughly assess your organization's needs and carefully evaluate the available options. By choosing the right solution and investing in proper training and support, you can unlock the full potential of Process Manufacturing Software, giving your business a competitive edge in the ever-evolving world of process manufacturing.