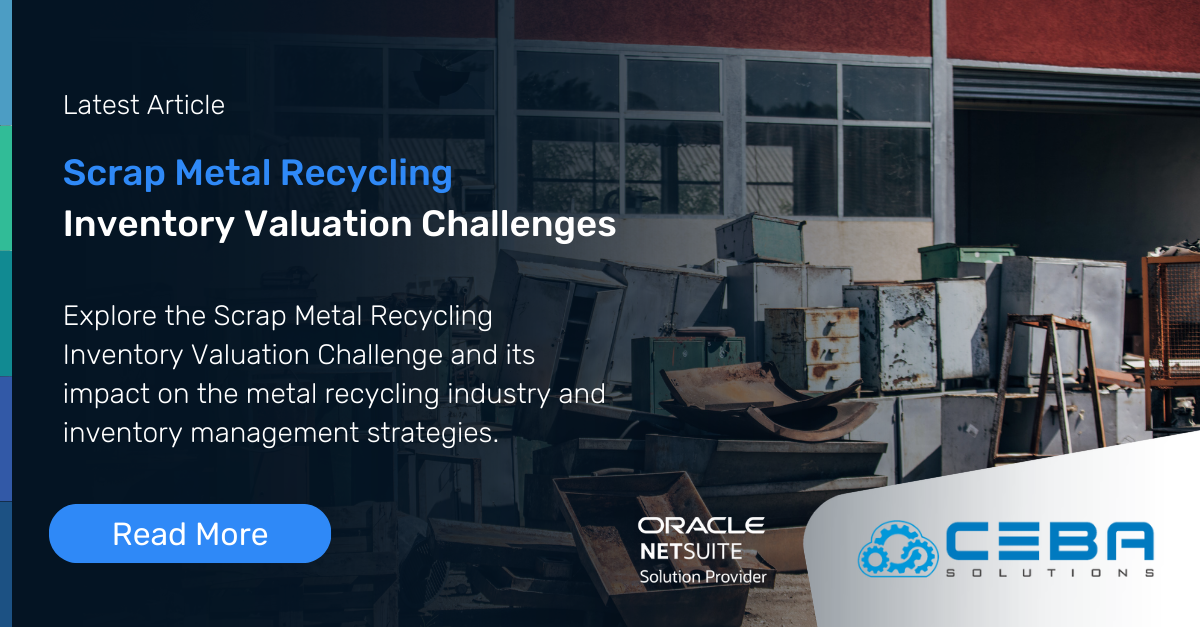
The Scrap Metal Recycling Inventory Valuation Challenge
The Scrap Metal Recycling Inventory Valuation Challenge
The scrap metal recycling industry transforms discarded materials into critical resources for construction and manufacturing industries. This transformation significantly contributes to sustainable economic practices but presents unique challenges for Chief Financial Officers (CFOs), especially in the precise valuation of scrap metal inventories. Unlike traditional manufacturing inventory, scrap metal features complex characteristics, including diverse material compositions, extreme price volatility, and intricate processing methods. Errors or inaccuracies in inventory valuation can lead to significant financial misstatements, impair profit analyses, misinform investment decisions, and risk non-compliance with stringent accounting standards. Consequently, accurate valuation methods that account for these complexities are indispensable, requiring CFOs to adopt specialized approaches and meticulous monitoring.
Navigating Market Price Volatility
Understanding the Impact of Market Dynamics
Scrap metal pricing is highly sensitive to global economic conditions, geopolitical developments, and fluctuations in supply and demand. The volatility within these markets can lead to substantial price changes within short periods, posing significant valuation challenges. For instance, a batch of copper scrap bought today might see its market value fluctuate considerably before it reaches the processing stage. Finance teams must maintain constant vigilance, continually monitoring market benchmarks and rapidly adjusting valuations to reflect the most current economic conditions accurately. Accurate documentation and clear communication of pricing benchmarks are essential to maintain transparency and meet auditing requirements.
Implementing Effective Risk Management
Given this volatility, financial managers must employ effective risk management strategies. Hedging strategies, such as futures contracts and options, help stabilize anticipated revenue streams and mitigate exposure to unpredictable market swings. Additionally, entering long-term agreements with fixed or formula-based pricing can significantly reduce risk. Proactively managing inventory turnover by minimizing excessive stock accumulation, especially of highly volatile metals, also limits the financial risks associated with price instability. A comprehensive risk management policy, clearly documented and regularly reviewed, ensures financial stability and regulatory compliance.
Grading as a Foundation of Accurate Valuation
Complexities in Scrap Metal Grading
Scrap metal encompasses a wide range of materials from ferrous metals like steel and iron to more valuable non-ferrous metals such as copper, aluminium, brass, and specialized alloys. Each material type and grade possesses distinct market values, influenced significantly by contamination levels, including plastics, dirt, rubber, and mixed alloys. The quality of incoming scrap directly impacts its valuation, necessitating a precise grading process. Misgrading materials can severely distort inventory values, influencing financial reporting accuracy and operational decision-making processes. Advanced technologies, including handheld X-Ray Fluorescence (XRF) analyzers, are invaluable for ensuring grading precision and enhancing inventory valuation reliability.
Standardizing Grading Practices
To mitigate grading inconsistencies, recycling operations must implement rigorous, standardized procedures for grading scrap metal upon receipt. Clearly documented guidelines and regular employee training ensure grading consistency and accuracy across teams. Regular audits of grading processes, supported by technological tools, are critical to maintaining high standards. Establishing systematic grading practices directly reduces valuation errors and facilitates accurate financial reporting, benefiting both operational efficiency and financial integrity.
"Accurate scrap metal valuation demands financial discipline, technological precision, and consistent grading standards to ensure transparency, manage risk, and uphold regulatory compliance in an increasingly volatile market." – Zabe Siddique, CEO – CEBA Solutions
Accurate Cost Accumulation Across Processing Stages
Challenges of Cost Allocation in Recycling
Accurately tracking and allocating costs in scrap metal recycling involves significant complexity, given multiple processing stages like sorting, shredding, refining, and transportation. These processes incur varied costs, including labor, equipment depreciation, energy consumption, and maintenance, complicating precise cost attribution. Additionally, the bulk and commingled nature of materials complicates direct cost tracking, particularly when processing stages overlap or merge. Yield losses due to moisture content, removal of contaminants, and processing inefficiencies further compound these challenges. Comprehensive cost tracking systems must account for these variables to ensure precise valuation and financial reporting.
Solutions for Effective Cost Tracking
Adopting specialized inventory management software can significantly enhance the precision of cost tracking and allocation across all stages of scrap metal processing. Such systems provide functionalities specifically designed to address the unique requirements of recycling operations, from initial material acquisition to final product dispatch. Implementing advanced technologies, such as automated sorting and drone-assisted inventory monitoring, further enhances accuracy. Regular reconciliations between physical stock and inventory data, coupled with detailed documentation of costs incurred at each stage, ensure comprehensive and transparent cost accumulation. This robust approach strengthens financial reporting accuracy and supports informed operational decision-making.
Evaluating and Implementing Accounting Methods
Comparison of Inventory Valuation Methods
Standard inventory valuation methods—FIFO, LIFO, Weighted Average Cost (WAC), and Specific Identification—each offer distinct advantages and limitations when applied to scrap metal recycling. FIFO aligns closely with recent market valuations but may be impractical due to the commingling of materials. LIFO, while potentially beneficial in aligning recent costs with revenue under US GAAP, remains prohibited under IFRS and equally difficult to administer accurately. The Weighted Average Cost method smooths fluctuations but risks obscuring short-term market dynamics crucial for precise profitability analysis. Specific Identification, suitable for unique, high-value items, is typically impractical for bulk scrap management due to intensive tracking demands.
Selecting Appropriate Valuation Methods
The selection of inventory valuation methods must align with operational realities and regulatory compliance obligations. Often, recycling firms find combining methods—for instance, using FIFO or WAC for bulk inventory while reserving Specific Identification for distinct, high-value items—most effective. Regular assessments of valuation methods, clearly documented and justified, support accurate financial reporting and operational efficiency. Ensuring consistent application of chosen methodologies reinforces regulatory compliance, minimizes auditing issues, and enhances stakeholder confidence in financial reports.
Standard inventory costing methods such as First-In, First-Out (FIFO), Last-In, First-Out (LIFO), and Weighted Average Cost (WAC) present distinct challenges when applied to the fluid and often indistinguishable nature of scrap metal stockpiles. The choice of method can significantly impact reported inventory values and cost of goods sold, especially in an environment of fluctuating prices. Companies must carefully evaluate which method, or combination thereof for different inventory types, best reflects the physical flow of goods and economic reality, while also complying with relevant accounting standards.
First-In, First-Out (FIFO) and Last-In, First-Out (LIFO)
The First-In, First-Out (FIFO) method assumes that the oldest inventory items are sold first. While conceptually simple, applying FIFO rigorously in a scrap yard where materials are often commingled in large piles can be practically impossible from a physical tracking perspective. Although it may reflect a more current valuation of ending inventory on the balance sheet during periods of rising prices, its core assumption often doesn't align with the actual physical movement of bulk scrap. Last-In, First-Out (LIFO), which assumes the newest inventory is sold first, can provide a better matching of current costs with current revenues in inflationary environments but is notably prohibited under International Financial Reporting Standards (IFRS). For entities reporting under US GAAP where LIFO is permissible, it can result in an understatement of inventory value on the balance sheet during periods of rising prices, though it may offer tax advantages. However, tracking distinct "layers" for LIFO can be just as, if not more, complex than FIFO for fungible scrap materials.
Weighted Average Cost (WAC)
The Weighted Average Cost (WAC) method calculates a new average cost for all units in inventory after each purchase, or on a periodic basis. This method tends to smooth out the effects of price volatility on the cost of goods sold and ending inventory values, which can be advantageous in the scrap metal industry. For commingled, indistinguishable items like bulk scrap, WAC is often considered more practical to implement than FIFO or LIFO, as it doesn't require tracking specific parcels of inventory. However, a potential drawback is that the WAC method may obscure the impact of recent, more volatile price movements on inventory values and profitability from specific transactions. Ensuring the weighted average calculation is consistently and accurately applied, especially with continuous inflows and outflows of material at various processing stages, remains a key operational challenge for finance departments.
Specific Identification Method
The Specific Identification method, which tracks the actual cost of each individual item in inventory, is theoretically the most accurate method as it matches the actual costs with the actual revenue. However, for the vast majority of scrap metal inventory, which is typically high-volume, low-unit-value (initially), and commingled, this method is generally impractical and cost-prohibitive to implement. It would require meticulous tracking of every piece or small batch of scrap from acquisition through all processing stages to final sale, an overwhelming task. The Specific Identification method might only be feasible for very distinct, high-value, or uniquely identifiable items within a scrap recycler's inventory, such as specialized alloys, intact machinery designated for resale, or large, easily traceable components, but it is not a viable primary valuation method for bulk scrap operations.
Strengthening Financial Integrity
Effective scrap metal inventory valuation demands a multifaceted approach addressing price volatility, grading accuracy, meticulous cost tracking, and appropriate inventory valuation methodologies. CFOs must adopt advanced technological solutions, implement rigorous operational protocols, and strategically manage risks to ensure financial accuracy and regulatory compliance. Comprehensive documentation and consistent application of accounting policies further bolster financial integrity. Ultimately, these robust valuation practices enable informed strategic decisions, promoting sustainable growth and operational stability within the scrap metal recycling industry.