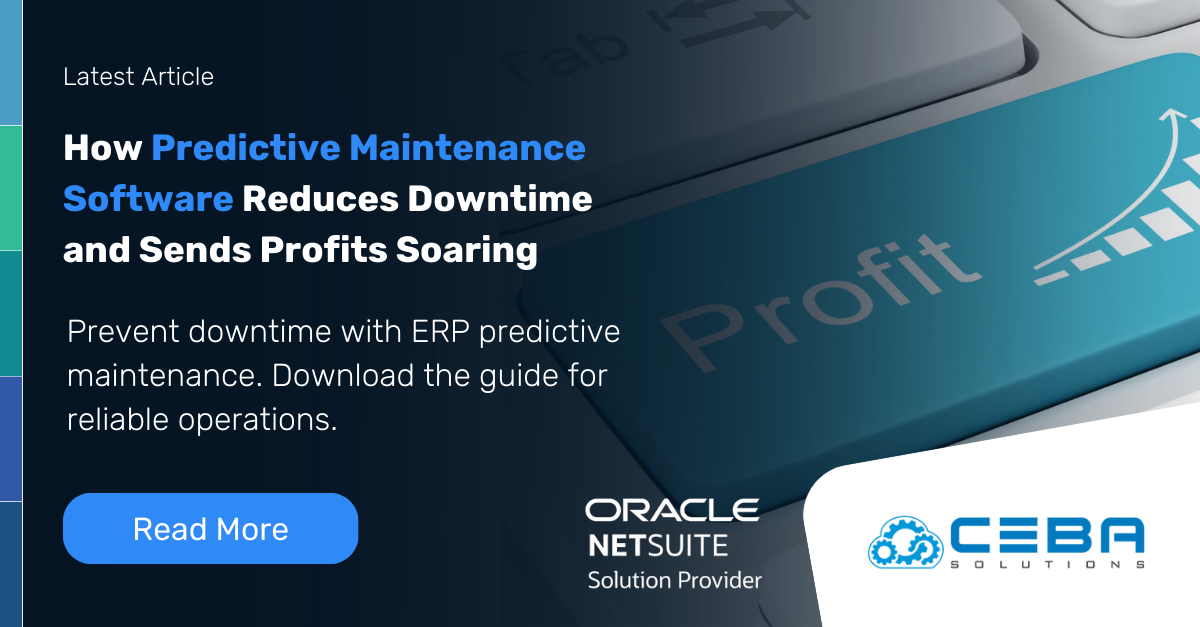
How Predictive Maintenance ERP Software Reduces Downtime and Sends Profits Soaring
How Predictive Maintenance ERP Software Reduces Downtime and Sends Profits Soaring
Predictive maintenance is a proactive approach to maintenance that aims to predict and prevent equipment failures before they occur. By using advanced technologies and data analysis techniques, predictive maintenance helps businesses optimize their maintenance practices and reduce downtime.
Importance of Predictive Maintenance in Heavy Industries
Predictive maintenance has become increasingly important in industries that rely heavily on equipment and machinery. Here are a few reasons why predictive maintenance is crucial:
Role of ERP Software in Predictive Maintenance
When it comes to predictive maintenance, implementing the right tools and technologies is crucial for its successful implementation. One such tool that plays a vital role in predictive maintenance is Enterprise Resource Planning (ERP) software.
ERP software not only streamlines maintenance processes but also enables real-time data collection and analysis, condition monitoring, automated work orders, inventory management, and parts procurement.
Streamlining Maintenance Processes
ERP software like NetSuite gives businesses a centralized system for managing maintenance activities, including creating and tracking work orders, scheduling tasks, and assigning resources. By streamlining these processes, software like NetSuite eliminates manual and paper-based systems, reducing administrative efforts and potential errors. This results in improved efficiency and productivity.
Real-Time Data Collection and Analysis
Modern ERP software can be integrated with various sensors, equipment, and systems to collect real-time data about asset performance, including temperature, vibration, and energy consumption. This data is then analyzed to identify maintenance trends, anomalies, and potential faults. By monitoring asset health in real-time, predictive maintenance can be performed proactively, preventing failures and minimizing downtime.
Condition Monitoring and Fault Predictions
With ERP software, condition monitoring becomes easier and more efficient. It allows for continuous monitoring of assets, capturing data on factors like temperature, pressure, and vibration. By analyzing this data, ERP systems can predict potential faults or failures before they occur, enabling proactive maintenance actions to be taken. This helps in minimizing unplanned breakdowns and reducing downtime.
Automated Work Orders and Scheduling
ERP software automates the creation, assignment, and scheduling of work orders based on defined criteria such as asset condition, priority, and resource availability. This eliminates manual intervention and reduces response time for maintenance tasks. By optimizing work order management, ERP software ensures that maintenance activities are executed in a timely manner, preventing delays and improving asset uptime.
Inventory Management and Parts Procurement
Managing inventory is critical for maintenance operations, and ERP software provides tools to optimize this process. It allows for accurate tracking of spare parts, managing stock levels, and generating purchase orders when inventory reaches a specified threshold. By ensuring the availability of the right parts at the right time, ERP software supports timely maintenance and reduces equipment downtime.
"In heavy industries, predictive maintenance is essential. With ERP software, we move from reactive fixes to proactive care, reducing downtime and saving costs. It's not just maintenance; it's smart maintenance." — Zabe Siddique, President of CEBA Solutions.
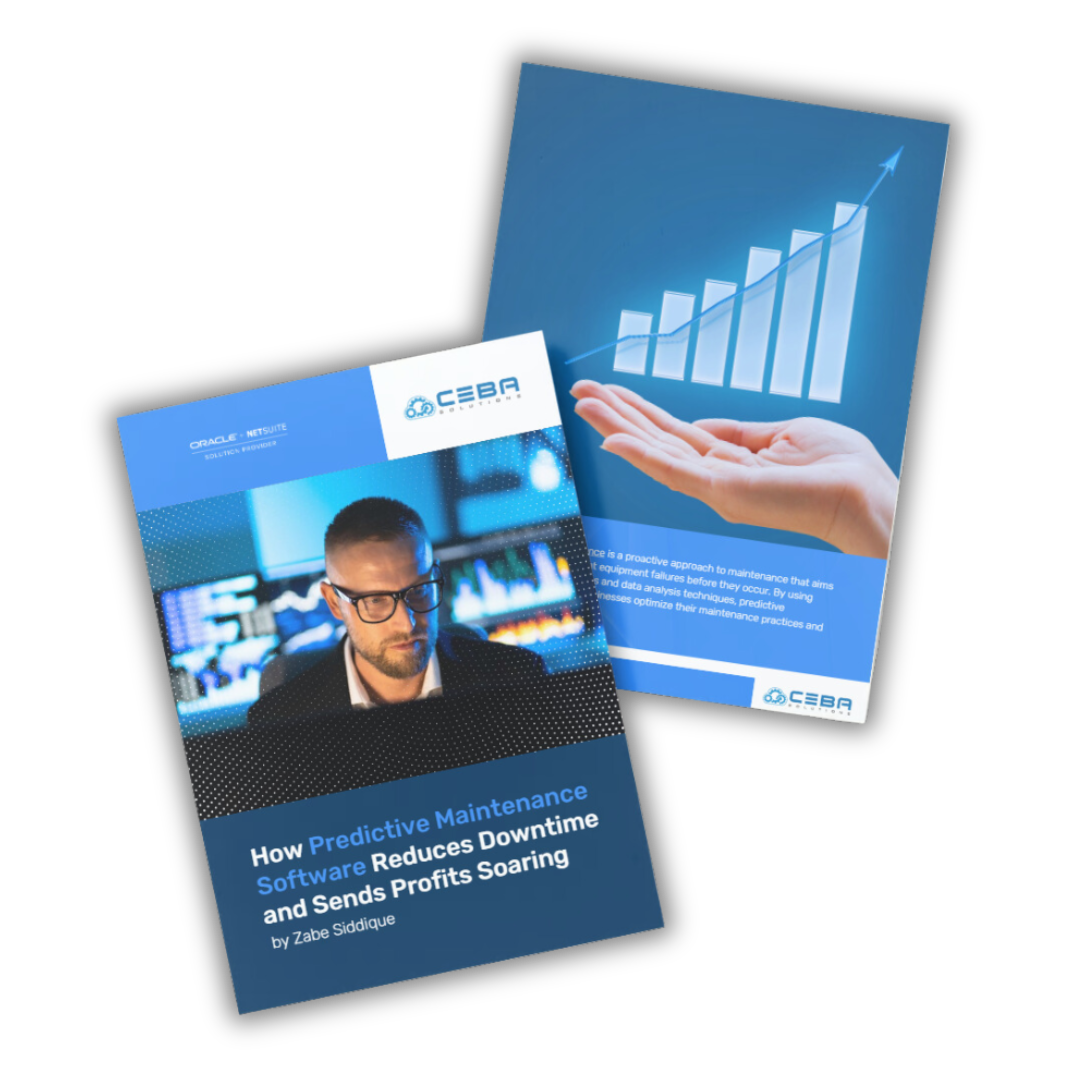
How Predictive Maintenance Software Reduces Downtime and Sends Profits Soaring
Download Here!
Benefits of Predictive Maintenance ERP Software
Predictive maintenance ERP software offers a wide range of benefits to industries across various sectors. By combining the power of predictive maintenance with an efficient ERP system, businesses can improve operational efficiency, and boost their profits.
Reduced Downtime and Unplanned Breakdowns
One of the primary advantages of predictive maintenance ERP software is its ability to detect potential equipment failures before they occur. By continuously monitoring the condition of assets and analyzing data in real-time, the software can identify early warning signs of impending failures. This proactive approach allows maintenance teams to take preventive action, such as scheduling maintenance tasks or replacing components, before a breakdown happens. As a result, businesses can minimize unplanned downtime, maximize equipment availability, and avoid costly production losses.
Lower Maintenance Costs and Increased Efficiency
Predictive maintenance ERP software helps optimize maintenance activities, leading to lower costs and increased efficiency. By analyzing real-time data from various sources, such as sensors, historical maintenance records, and equipment performance data, the software can identify patterns and trends that can help optimize maintenance schedules. This ensures that maintenance tasks are carried out only when necessary, avoiding unnecessary expenses and reducing the time required to complete them. Moreover, by focusing maintenance efforts on critical assets and prioritizing tasks, businesses can allocate their resources more effectively and improve overall operational efficiency.
Improved Equipment Reliability and Lifespan
Regular maintenance activities and timely repairs help improve the reliability and lifespan of equipment. With predictive maintenance ERP software, businesses can ensure that maintenance tasks are performed at the right time, using the right resources. By addressing potential issues proactively, the software helps reduce the likelihood of equipment failures and extends the lifespan of assets. This not only saves businesses the costs of replacing equipment prematurely but also enhances the reliability of critical systems, leading to increased productivity and customer satisfaction.
Enhanced Safety and Compliance
Safety is a top priority in any industry, and predictive maintenance ERP software plays a crucial role in ensuring a safe working environment. By monitoring equipment conditions and identifying potential safety risks, the software allows businesses to address hazards before they escalate into accidents. Moreover, the software can help track and manage compliance requirements, such as inspections and certifications, ensuring that all necessary safety regulations are adhered to. This helps businesses maintain a safe working environment, avoid penalties, and protect the well-being of their employees.
Optimized Inventory and Spare Parts Management
Inventory management can be a complex task for industries that rely on various equipment and spare parts. Predictive maintenance ERP software streamlines this process by monitoring the usage and performance of assets in real-time. It can automatically generate purchase orders for spare parts when stock levels are low or forecasted maintenance activities require specific components. This eliminates the need for manual tracking and reduces the risk of running out of critical spare parts. Additionally, by optimizing inventory levels, businesses can reduce carrying costs and improve cash flow.
Better Decision Making and Resource Planning
By providing real-time insights and comprehensive data analysis, predictive maintenance ERP software empowers businesses with better decision-making capabilities. Managers can access dashboards and reports that highlight key performance indicators, equipment health, and maintenance trends. This information enables them to make data-driven decisions regarding resource allocation, equipment replacement, and process improvement. Additionally, the software aids in long-term planning by providing accurate maintenance cost projections and asset lifecycle information. This helps businesses optimize their resources, reduce unnecessary expenses, and make informed decisions that align with their strategic goals.
"In industries reliant on heavy machinery, predictive maintenance ERP software is a game-changer. It minimizes downtime, lowers maintenance costs, and ensures safety, transforming data into actionable plans for smarter resource allocation and higher profits."— Zabe Siddique, President of CEBA Solutions.
Implementing Predictive Maintenance ERP Software
Implementing a predictive maintenance ERP software is a strategic decision that can transform the way industries manage their maintenance operations. By utilizing advanced technology, real-time data, and automation, businesses can significantly reduce downtime, increase efficiency, and achieve higher profits. However, implementing this software requires careful planning, consideration, and proper execution. In this section, we will explore the key steps involved in implementing predictive maintenance ERP software.
Identifying System Requirements
Before implementing any new software, it's crucial to identify your specific system requirements. This involves assessing your current maintenance processes, understanding the pain points, and defining your objectives. Consider the following questions:
- What are the key challenges you are facing in maintenance management?
- What are your primary goals for implementing predictive maintenance ERP software?
- How will this software align with your overall business goals and objectives?
By clearly defining your requirements, you will be able to select the right software solution that meets your needs.
Choosing the Right ERP Software Solution
Choosing the right ERP software solution is a critical step in implementing predictive maintenance. Consider the following factors while evaluating different options:
Functionality
Ensure that the software offers features such as real-time data collection, analysis, automated work orders, condition monitoring, and inventory management.
Scalability
Choose a solution that can grow with your business and accommodate future needs.
Integration
Ensure that the ERP software can integrate seamlessly with your existing systems, such as asset management, CMMS (Computerized Maintenance Management System), and IoT devices.
Usability
Look for software that is user-friendly and intuitive, making it easy for your maintenance team to adapt and utilize effectively.
Vendor Support
Evaluate the vendor's reputation, track record, and customer support services to ensure a smooth implementation and ongoing support.
Integration with Existing Systems
To maximize the benefits of predictive maintenance ERP software, it is crucial to integrate it with your existing systems. Integration allows data to flow seamlessly between different systems, empowering you with a comprehensive view of your maintenance operations. Consider the following integration points:
Asset Management
Integrate the ERP software with your asset management system to centralize asset information and enable proactive maintenance planning.
CMMS
Connect the ERP software with your CMMS to streamline work order generation, scheduling, and maintenance execution.
IoT Devices
Integrate the ERP software with IoT devices for real-time condition monitoring and predictive analytics.
Data Analytics Platforms
Connect the ERP software to data analytics platforms for advanced predictive maintenance insights.
Challenges and Considerations
Implementing predictive maintenance ERP software comes with its fair share of challenges and considerations. To ensure a successful integration and maximize the benefits of the software, businesses need to address the following factors:
Data Quality and Integration
One of the main challenges is ensuring the quality and accuracy of the data collected from various sources. The software relies heavily on data to make accurate predictions and preventive maintenance recommendations. If the data is incomplete, inconsistent, or of poor quality, it can negatively impact the effectiveness of the system.
Integrating the ERP software with existing systems can also be a complex task. The software needs to seamlessly integrate with other software and equipment to gather data and provide real-time insights. Proper data integration is crucial for effective predictive maintenance.
Technological Infrastructure
The success of predictive maintenance ERP software depends heavily on a robust and reliable technological infrastructure. This includes having a stable network connection, sufficient computing power, and storage capacity to handle large volumes of data.
Upgrading existing infrastructure may be necessary to support the ERP software's requirements. This can involve investing in hardware upgrades, network expansions, and additional storage solutions.
Resource Allocation and Budgeting
Implementing predictive maintenance ERP software requires careful consideration of resources and budget allocation. Companies need to allocate sufficient resources for software deployment, employee training, system maintenance, and ongoing support.
It is important to assess the financial impact and return on investment (ROI) of implementing the software. While predictive maintenance software can lead to cost savings and increased efficiency in the long run, there may be initial upfront costs and budget adjustments required.
Security and Data Privacy
With the increasing reliance on data and cloud-based solutions, ensuring the security and privacy of sensitive information becomes paramount. Businesses need to have robust security measures in place to protect data from unauthorized access or breaches.
Compliance with data protection regulations, such as the General Data Protection Regulation (GDPR), is crucial. Businesses must ensure that their predictive maintenance ERP software adheres to these regulations to maintain customer trust and avoid legal issues.
Organizational Readiness
Implementing predictive maintenance ERP software requires the commitment and buy-in of all stakeholders within the organization. Resistance to change and lack of training can hinder the successful implementation of the system.
It is essential to assess the organization's readiness for change and provide appropriate training and support to employees. This includes educating employees on the benefits of the software and addressing any concerns or resistance they may have.
By addressing these challenges and considerations, businesses can overcome potential obstacles and fully leverage the power of predictive maintenance ERP software. It is crucial to carefully plan and strategize the implementation process to ensure a smooth transition and maximize the benefits for long-term success.
Conclusion
Implementing predictive maintenance ERP software can significantly reduce downtime and increase profits for businesses in various industries. The integration of ERP software with predictive maintenance techniques helps streamline maintenance processes, collect and analyze real-time data, predict faults, and automate work orders. As a result, companies experience reduced downtime, lower maintenance costs, improved equipment reliability, enhanced safety, optimized inventory management, and improved decision-making.
NetSuite, a leading provider of ERP, CRM, and inventory management solutions, offers a comprehensive suite of tools to support businesses in implementing predictive maintenance strategies. NetSuite can help streamline maintenance processes, collect and analyze real-time data, and optimize inventory management.
If you are interested in learning more about how NetSuite can help streamline your maintenance strategies, feel free to reach out to our team for more information.