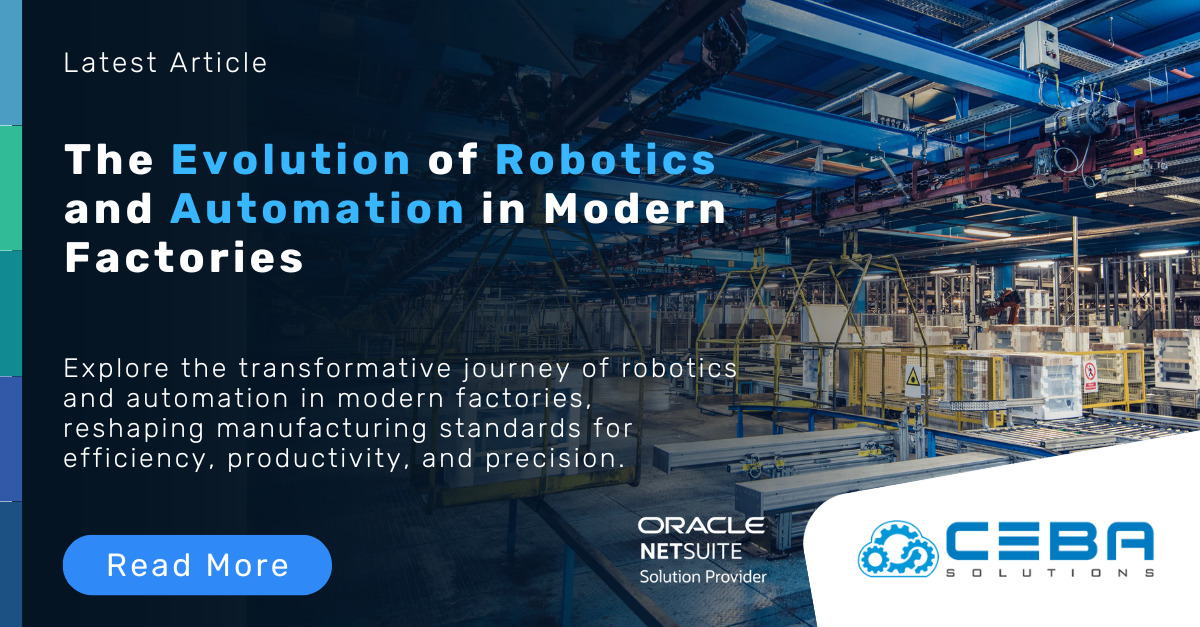
The Evolution of Robotics and Automation in Modern Factories
The Evolution of Robotics and Automation in Modern Factories
The modern manufacturing landscape is undergoing a profound transformation, driven by the relentless march of robotics and automation. These technologies have revolutionized how factories operate, enhancing efficiency, productivity, and flexibility while reducing costs and errors. The evolution of robotics and automation in modern factories marks a pivotal chapter in the history of industrial innovation, reshaping industries and creating new opportunities for growth and development.
Early Beginnings: The First Industrial Robots
The journey of robotics in manufacturing began in the mid-20th century with the advent of the first industrial robots. In 1961, Unimate, the world's first industrial robot, was installed at a General Motors plant. Developed by George Devol and Joseph Engelberger, Unimate was designed to perform repetitive tasks such as welding and material handling, tasks that were dangerous and tedious for human workers. This marked the beginning of the integration of robotics into manufacturing processes, laying the foundation for future advancements.
The Rise of Automation: Enhancing Efficiency and Productivity
Throughout the 1970s and 1980s, advancements in robotics and automation technologies continued to accelerate. The development of programmable logic controllers (PLCs) allowed for greater automation and control of manufacturing processes. Robots became more sophisticated, capable of performing a wider range of tasks with increased precision and speed.
During this period, the automotive industry emerged as a key adopter of robotics and automation. Assembly lines became more automated, with robots taking on tasks such as painting, welding, and assembling parts. This shift not only improved efficiency and productivity but also enhanced product quality and worker safety.
The Digital Revolution: Integrating Robotics with Digital Technologies
The late 20th and early 21st centuries witnessed the digital revolution, which brought about significant advancements in robotics and automation. The integration of digital technologies such as sensors, computer vision, and artificial intelligence (AI) transformed industrial robots into intelligent systems capable of complex decision-making and adaptability.
- Sensors and Computer Vision:Sensors and computer vision technologies enabled robots to perceive and interact with their environment. Robots could now identify objects, navigate spaces, and perform tasks with a high degree of accuracy. These capabilities allowed for the automation of tasks that were previously thought to be too complex for machines.
- Artificial Intelligence and Machine Learning:The incorporation of AI and machine learning further enhanced the capabilities of industrial robots. AI algorithms allowed robots to learn from data, optimize processes, and make real-time decisions. Machine learning enabled predictive maintenance, where robots could analyze data to predict equipment failures and schedule maintenance before issues arose, minimizing downtime and improving efficiency.
- Collaborative Robots (Cobots):The advent of collaborative robots, or cobots, marked a significant milestone in the evolution of robotics in manufacturing. Unlike traditional industrial robots, which operated in isolation from human workers, cobots were designed to work alongside humans. Cobots are equipped with advanced safety features, such as force sensing and collision detection, allowing them to collaborate with human workers safely. This collaboration enhanced flexibility and productivity, enabling manufacturers to optimize both human and robotic capabilities.
Industry 4.0: The Smart Factory
The concept of Industry 4.0, also known as the Fourth Industrial Revolution, encapsulates the next stage in the evolution of robotics and automation. Industry 4.0 envisions smart factories where cyber-physical systems, the Internet of Things (IoT), and big data analytics are integrated to create highly efficient and adaptable manufacturing environments.
- Cyber-Physical Systems:Cyber-physical systems (CPS) integrate physical machinery with digital technologies, creating interconnected networks of devices that communicate and coordinate with each other. In smart factories, CPS enable real-time monitoring and control of manufacturing processes, optimizing performance and reducing waste.
- Internet of Things (IoT):IoT devices collect and transmit data from various parts of the manufacturing process. This data is analyzed to gain insights into operations, identify inefficiencies, and predict maintenance needs. IoT enhances visibility and transparency, allowing manufacturers to make data-driven decisions and respond quickly to changing conditions.
- Big Data Analytics:The vast amounts of data generated by smart factories are analyzed using big data analytics. These analytics provide valuable insights into production processes, supply chain management, and customer preferences. By leveraging big data, manufacturers can optimize operations, improve product quality, and enhance customer satisfaction.
The Benefits of Robotics and Automation in Modern Factories
The integration of robotics and automation in modern factories offers numerous benefits, driving significant improvements in various aspects of manufacturing:
- Increased Productivity:Robots and automated systems can operate continuously without fatigue, significantly increasing production rates. Automation reduces cycle times and minimizes downtime, leading to higher overall productivity.
- Enhanced Quality:The precision and consistency of robots result in higher product quality. Automated systems can perform tasks with a high degree of accuracy, reducing errors and defects. This consistency is particularly valuable in industries with stringent quality standards, such as automotive and electronics manufacturing.
- Cost Savings:While the initial investment in robotics and automation can be substantial, the long-term cost savings are significant. Automation reduces labor costs, minimizes waste, and optimizes resource utilization. Predictive maintenance also helps avoid costly equipment failures and production stoppages.
- Improved Safety:Robots can perform hazardous tasks, such as handling toxic materials or operating in extreme conditions, reducing the risk to human workers. Automation also minimizes the likelihood of workplace accidents caused by human error.
- Flexibility and Adaptability:Modern robots are highly adaptable and can be reprogrammed for different tasks, providing manufacturers with greater flexibility. This adaptability is crucial in industries with high variability in production requirements or frequent changes in product design.
Challenges and Future Directions
Despite the many benefits, the integration of robotics and automation in manufacturing also presents challenges:
- High Initial Investment:The cost of acquiring and implementing advanced robotics and automation systems can be prohibitive for some manufacturers, particularly small and medium-sized enterprises (SMEs).
- Skills Gap:The shift towards automated manufacturing requires a workforce with new skills in robotics, programming, and data analysis. Addressing the skills gap through training and education is essential for the successful adoption of these technologies.
- Integration and Interoperability:Integrating new automation systems with existing infrastructure can be complex and may require significant changes to processes and workflows. Ensuring interoperability between different systems and technologies is crucial for seamless operations.
Conclusion
The evolution of robotics and automation in modern factories has transformed the manufacturing industry, offering unprecedented levels of efficiency, productivity, and quality. From the early days of industrial robots to the era of smart factories and Industry 4.0, the advancements in robotics and automation continue to drive innovation and reshape the manufacturing landscape. As technology continues to evolve, the future of manufacturing promises even greater opportunities for growth, sustainability, and competitiveness. Embracing these advancements and addressing the associated challenges will be key to navigating the next wave of industrial transformation.