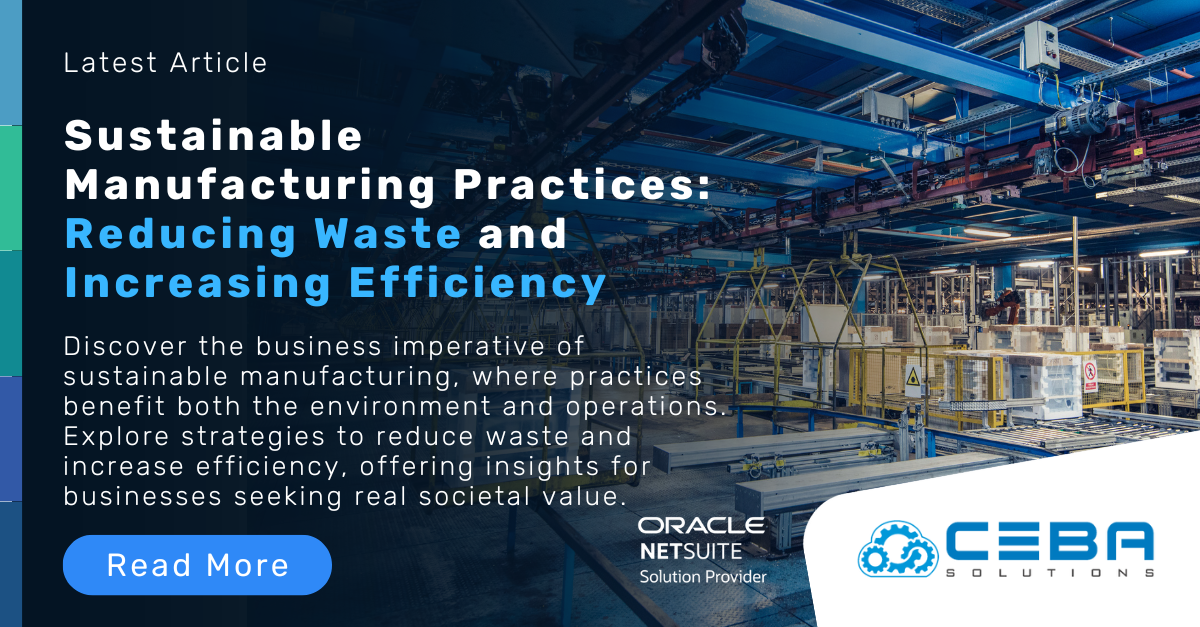
Sustainable Manufacturing Practices: Reducing Waste and Increasing Efficiency
Sustainable Manufacturing Practices: Reducing Waste and Increasing Efficiency
In the quest for a greener and more sustainable future, the manufacturing sector plays a pivotal role. As global environmental concerns intensify, companies are increasingly adopting sustainable manufacturing practices to minimize waste, reduce resource consumption, and enhance overall efficiency. These practices not only contribute to environmental conservation but also offer significant economic and operational benefits. This article explores key sustainable manufacturing practices, their benefits, and how they are reshaping the industry towards a more sustainable future.
The Importance of Sustainable Manufacturing
Sustainable manufacturing involves creating products through economically-sound processes that minimize negative environmental impacts while conserving energy and natural resources. This approach also enhances employee, community, and product safety. The shift towards sustainable manufacturing is driven by several factors:
- Environmental Responsibility: Reducing the ecological footprint of manufacturing activities is essential for combating climate change, conserving biodiversity, and ensuring the sustainability of natural resources.
- Regulatory Compliance: Governments worldwide are enacting stricter environmental regulations, requiring manufacturers to adopt sustainable practices to avoid penalties and comply with legal standards.
- Economic Benefits: Sustainable manufacturing can lead to cost savings through improved resource efficiency, waste reduction, and energy conservation. It also opens up new market opportunities as consumers increasingly prefer eco-friendly products.
- Corporate Reputation: Demonstrating a commitment to sustainability enhances a company’s brand image and reputation, attracting environmentally-conscious consumers, investors, and partners.
Key Sustainable Manufacturing Practices
- Lean Manufacturing:Lean manufacturing focuses on minimizing waste and maximizing productivity. It involves identifying and eliminating non-value-added activities in the production process. Key lean principles include:
- Just-In-Time (JIT): Producing only what is needed, when it is needed, to reduce inventory waste and improve resource utilization.
- Kaizen (Continuous Improvement): Encouraging continuous, incremental improvements in processes to enhance efficiency and reduce waste.
- 5S Methodology: Organizing the workplace to improve efficiency and reduce waste through sorting, setting in order, shining, standardizing, and sustaining practices.
- Circular Economy:The circular economy model emphasizes the importance of designing products and processes that enable materials to be reused, refurbished, remanufactured, or recycled. Key strategies include:
- Design for Disassembly: Designing products in a way that makes it easy to disassemble and recover valuable components and materials.
- Product-as-a-Service: Shifting from selling products to offering them as services, encouraging manufacturers to take responsibility for the entire product lifecycle.
- Material Recovery: Implementing processes to recover and recycle materials from end-of-life products.
- Energy Efficiency:Reducing energy consumption is a critical aspect of sustainable manufacturing. Strategies to improve energy efficiency include:
- Energy Audits: Conducting regular energy audits to identify inefficiencies and opportunities for energy savings.
- Energy-Efficient Equipment: Investing in energy-efficient machinery, lighting, and HVAC systems.
- Renewable Energy: Utilizing renewable energy sources, such as solar, wind, and biomass, to power manufacturing operations.
- Waste Minimization:Effective waste management practices reduce the amount of waste generated and promote recycling and reuse. Key practices include:
- Zero Waste Initiatives: Aiming to divert all waste from landfills through recycling, composting, and other waste diversion strategies.
- Process Optimization: Streamlining production processes to minimize scrap, defects, and overproduction.
- Industrial Symbiosis: Collaborating with other industries to use waste or by-products from one process as raw materials for another.
- Water Conservation:Reducing water consumption and improving water management practices are essential for sustainable manufacturing. Strategies include:
- Water Recycling and Reuse: Implementing systems to treat and reuse wastewater within the manufacturing process.
- Efficient Water Use: Installing water-efficient fixtures and equipment to reduce water usage.
- Rainwater Harvesting: Collecting and using rainwater for non-potable purposes within the facility.
- Green Supply Chain Management:Extending sustainability practices to the supply chain ensures that environmental considerations are integrated into every stage of the product lifecycle. Key practices include:
- Supplier Sustainability Audits: Assessing and selecting suppliers based on their environmental performance and sustainability practices.
- Sustainable Sourcing: Sourcing raw materials from sustainable and ethical sources.
- Collaborative Logistics: Optimizing transportation and logistics to reduce carbon emissions and improve efficiency.
Benefits of Sustainable Manufacturing
Adopting sustainable manufacturing practices offers a range of benefits:
- Cost Savings: Improved efficiency and waste reduction lead to significant cost savings in materials, energy, and waste management.
- Enhanced Competitiveness: Companies that adopt sustainable practices can differentiate themselves in the market, attract eco-conscious consumers, and tap into new business opportunities.
- Regulatory Compliance: Adhering to environmental regulations avoids potential fines and legal issues, ensuring smooth business operations.
- Employee Satisfaction: Sustainable practices often result in safer and healthier working conditions, improving employee morale and retention.
- Innovation and Growth: Sustainability drives innovation, leading to the development of new products, processes, and business models that can spur growth and profitability.
Challenges and Solutions
While the transition to sustainable manufacturing offers significant benefits, it also presents challenges:
- Initial Costs: The upfront investment in new technologies, equipment, and training can be substantial. However, long-term savings and efficiencies often offset these initial costs.
- Complexity: Implementing sustainable practices requires a comprehensive understanding of the entire production process and supply chain. Companies can overcome this by adopting a phased approach and leveraging expert guidance.
- Cultural Change: Shifting to a sustainability-focused mindset can be challenging for organizations. Encouraging employee involvement and providing continuous education and training can foster a culture of sustainability.
Conclusion
Sustainable manufacturing practices are essential for reducing waste, increasing efficiency, and driving long-term business success. By adopting lean manufacturing, embracing the circular economy, improving energy and water efficiency, minimizing waste, and implementing green supply chain management, manufacturers can significantly reduce their environmental impact while enhancing productivity and competitiveness. As the global focus on sustainability intensifies, companies that proactively adopt and integrate sustainable practices will be better positioned to thrive in the evolving marketplace and contribute to a more sustainable future for all.