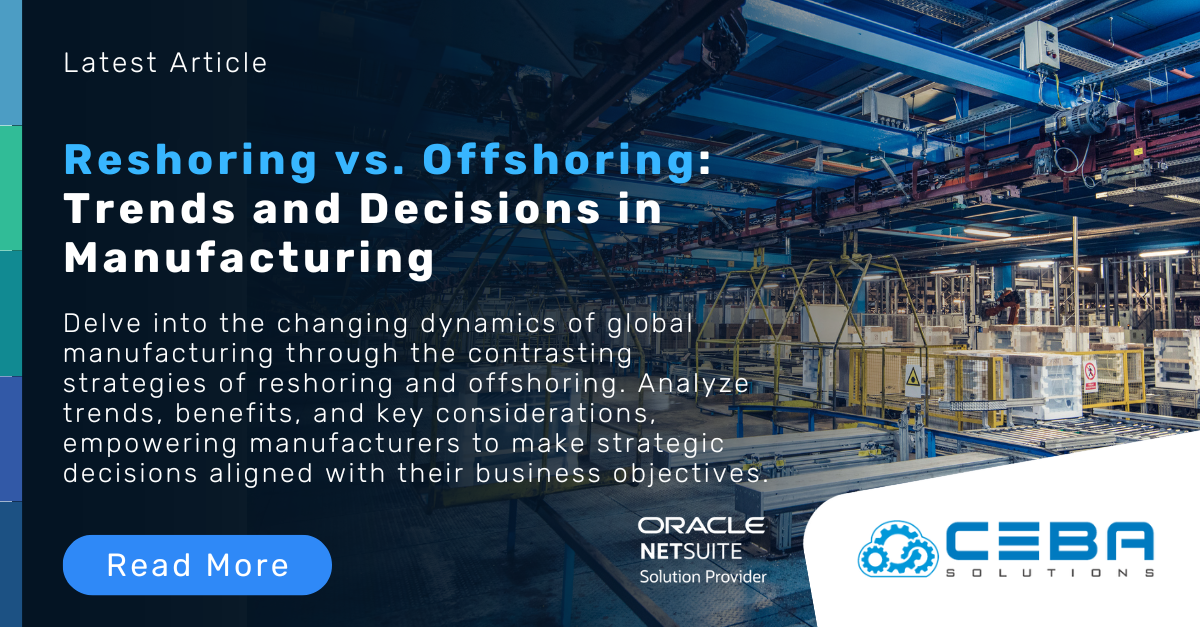
Reshoring vs. Offshoring: Trends and Decisions in Manufacturing
Reshoring vs. Offshoring: Trends and Decisions in Manufacturing
In the dynamic world of manufacturing, the strategic decisions about where to locate production facilities are crucial. These decisions can significantly impact a company's cost structure, supply chain efficiency, and overall competitiveness. Two primary strategies have long been debated: offshoring and reshoring. Offshoring involves relocating manufacturing operations to foreign countries, typically to capitalize on lower labor costs, while reshoring brings production back to the company's home country. This article explores the trends and factors influencing these strategic choices in manufacturing, examining the benefits, challenges, and future outlook of both offshoring and reshoring.
Understanding Offshoring and Reshoring
Offshoring: This strategy became popular in the late 20th and early 21st centuries as companies sought to reduce production costs by taking advantage of cheaper labor, raw materials, and favorable regulatory environments abroad. Countries like China, India, and Mexico emerged as major manufacturing hubs, offering significant cost advantages to companies willing to move their operations overseas.
Reshoring: In contrast, reshoring involves bringing manufacturing operations back to the home country. This trend has gained momentum in recent years due to various factors, including rising labor costs in traditional offshore locations, geopolitical tensions, supply chain disruptions, and a renewed focus on local manufacturing capabilities.
Trends in Manufacturing Decisions
- Cost Considerations:
- Offshoring: Historically, the primary driver for offshoring has been the significant cost savings, particularly in labor. However, the cost advantage has been narrowing due to rising wages in countries like China. Additionally, hidden costs such as transportation, tariffs, and quality control issues have made offshoring less attractive.
- Reshoring: Advances in automation and robotics have reduced the labor cost differential, making reshoring more economically viable. Additionally, reshoring can reduce shipping costs and lead times, contributing to overall cost savings.
- Supply Chain Resilience:
- Offshoring: While offshoring can lower costs, it can also make supply chains longer and more complex, increasing the risk of disruptions due to geopolitical instability, natural disasters, and pandemics. The COVID-19 pandemic, for example, exposed the vulnerabilities of global supply chains and highlighted the need for more resilient supply chain strategies.
- Reshoring: By bringing production closer to the end market, reshoring can enhance supply chain resilience and reduce dependency on foreign suppliers. Shorter supply chains are easier to manage and less susceptible to global disruptions, improving overall reliability.
- Quality and Control:
- Offshoring: Ensuring consistent quality and maintaining control over production processes can be challenging in offshore locations due to differences in standards, communication barriers, and logistical complexities. Quality issues can lead to increased costs and damage to a company's reputation.
- Reshoring: Reshoring can improve quality control by enabling closer oversight of manufacturing processes. Proximity to the production site allows for more frequent inspections, quicker responses to issues, and better alignment with company standards.
- Innovation and Speed to Market:
- Offshoring: The distance between design and production teams can hinder collaboration and slow down the innovation process. Additionally, long lead times can delay the introduction of new products to the market.
- Reshoring: Locating production facilities closer to research and development (R&D) centers can foster better collaboration and accelerate innovation. Shorter lead times enhance a company's ability to respond quickly to market changes and customer demands.
- Economic and Political Factors:
- Offshoring: Offshoring can be influenced by favorable trade agreements, tax incentives, and regulatory environments in foreign countries. However, it is also subject to risks such as changes in trade policies, tariffs, and political instability.
- Reshoring: Reshoring can be encouraged by government policies that promote local manufacturing through incentives, tax breaks, and subsidies. Additionally, a focus on national security and reducing reliance on foreign supply chains has bolstered support for reshoring initiatives.
Challenges of Reshoring and Offshoring
Despite the benefits, both reshoring and offshoring come with their own set of challenges:
- Reshoring:
- Higher initial costs for setting up or upgrading domestic facilities.
- Potential skills gap in the local workforce for advanced manufacturing technologies.
- Higher operating costs compared to traditional offshore locations.
- Navigating local regulatory requirements and compliance issues.
- Offshoring:
- Increased logistical complexity and transportation costs.
- Potential quality control issues and intellectual property risks.
- Vulnerability to geopolitical tensions and trade policy changes.
- Cultural and language barriers impacting communication and management.
Future Outlook: Balancing Reshoring and Offshoring
The future of manufacturing will likely involve a balanced approach, leveraging the strengths of both reshoring and offshoring to optimize operations. Companies may adopt a hybrid model that includes:
- Nearshoring: Moving production to nearby countries with favorable costs and logistics, such as Mexico for U.S. companies or Eastern Europe for Western European companies. Nearshoring offers a middle ground between the cost savings of offshoring and the logistical advantages of reshoring.
- Distributed Manufacturing: Utilizing a network of smaller, strategically located manufacturing facilities to reduce risks and improve flexibility. Distributed manufacturing can enhance supply chain resilience and allow companies to respond more quickly to local market demands.
- Digital Transformation: Investing in advanced manufacturing technologies such as automation, AI, and IoT to enhance productivity, reduce costs, and improve quality. Digital transformation can make domestic manufacturing more competitive and support the reshoring trend.
- Sustainability Focus: Considering the environmental impact of manufacturing decisions and prioritizing sustainable practices. Both reshoring and offshoring strategies can benefit from a focus on sustainability, such as reducing carbon footprints and minimizing waste.
Conclusion
The decision between reshoring and offshoring is complex and multifaceted, influenced by a range of economic, operational, and strategic factors. While offshoring has traditionally been driven by cost savings, the rise of automation, the need for supply chain resilience, and changing geopolitical landscapes are driving a shift towards reshoring. By carefully evaluating the benefits and challenges of each strategy and adopting a balanced approach, manufacturers can navigate the evolving landscape and position themselves for long-term success.