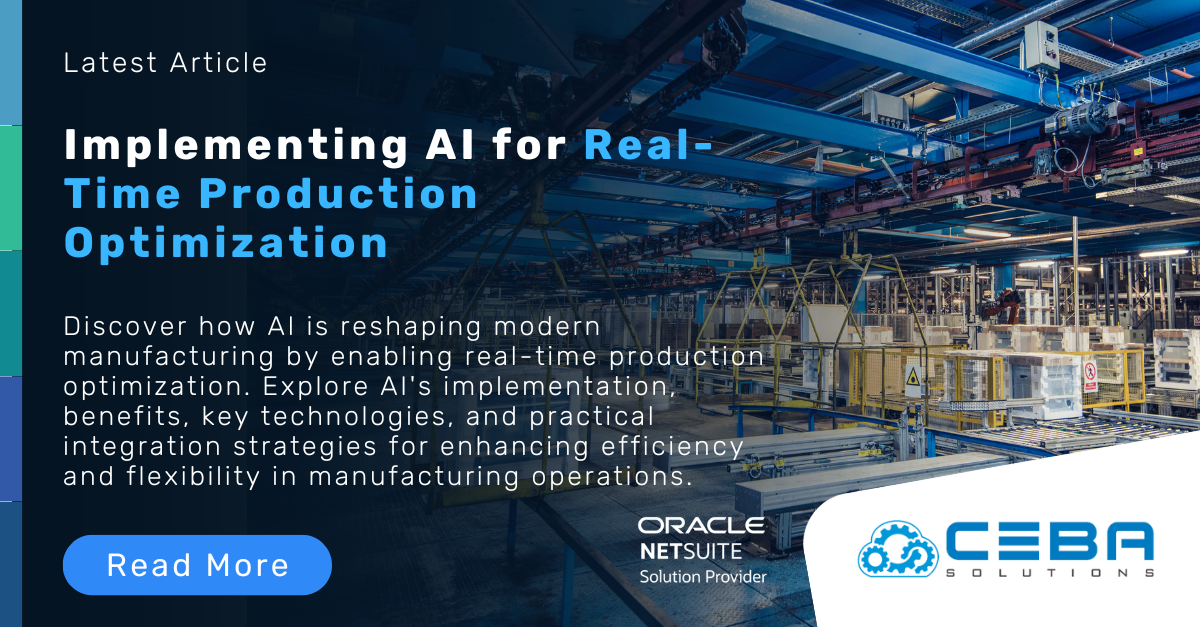
Implementing AI for Real-Time Production Optimization
Implementing AI for Real-Time Production Optimization
In today’s highly competitive manufacturing environment, optimizing production processes in real-time is essential for maintaining efficiency, reducing costs, and enhancing product quality. Artificial intelligence (AI) has emerged as a powerful tool in achieving these goals, offering the capability to analyze vast amounts of data, predict outcomes, and make decisions autonomously. Implementing AI for real-time production optimization can transform manufacturing operations, providing significant advantages over traditional methods. This article explores the benefits, strategies, and challenges of integrating AI into production processes for real-time optimization.
The Benefits of AI in Production Optimization
- Increased Efficiency:AI systems can analyze data from various stages of the production process to identify inefficiencies and suggest improvements. By continuously monitoring and adjusting operations, AI can help optimize resource allocation, minimize waste, and streamline workflows, leading to increased overall efficiency.
- Predictive Maintenance:AI-driven predictive maintenance uses data from sensors and machine learning algorithms to predict equipment failures before they occur. This proactive approach reduces downtime, extends the lifespan of machinery, and lowers maintenance costs by addressing issues before they lead to costly breakdowns.
- Enhanced Quality Control:AI can enhance quality control by detecting defects and anomalies in real-time. Machine vision systems powered by AI can inspect products at high speeds, ensuring that only items meeting quality standards proceed down the production line. This reduces waste and improves the consistency of the final product.
- Dynamic Supply Chain Management:AI enables dynamic supply chain management by providing real-time visibility into inventory levels, supplier performance, and logistics. This allows manufacturers to respond quickly to changes in demand, avoid stockouts, and reduce excess inventory, optimizing the entire supply chain.
- Adaptive Process Control:AI systems can adaptively control production processes by continuously learning from data and adjusting parameters to maintain optimal performance. This leads to more flexible and responsive manufacturing operations, capable of adjusting to variations in input materials or changing market conditions.
Strategies for Implementing AI in Real-Time Production Optimization
- Data Collection and Integration:The foundation of any AI implementation is robust data collection and integration. Sensors and IoT devices should be installed throughout the production line to capture data on various parameters such as temperature, pressure, speed, and quality metrics. This data needs to be integrated into a centralized system where it can be accessed and analyzed by AI algorithms.
- Building a Data Infrastructure:A solid data infrastructure is essential for supporting AI applications. This includes high-speed data storage, processing capabilities, and secure data transmission. Cloud computing platforms can provide scalable resources for handling large volumes of data and running complex AI models.
- Developing Machine Learning Models:Developing effective machine learning models requires selecting the right algorithms and training them on historical and real-time data. This involves data preprocessing, feature selection, and model validation to ensure accuracy and reliability. Collaboration with data scientists and AI experts can help in creating robust models tailored to specific production processes.
- Implementing Real-Time Analytics:Real-time analytics involves deploying AI models that can process data and generate insights on the fly. This requires integrating AI systems with production control systems to enable real-time decision-making. Dashboards and visualization tools can help operators monitor performance and take immediate action based on AI-generated recommendations.
- Continuous Learning and Improvement:AI systems should be designed to continuously learn and improve from new data. Implementing feedback loops where AI models are regularly updated with the latest data ensures that the system adapts to changing conditions and maintains optimal performance. Regularly retraining models helps in addressing drift and improving accuracy over time.
- Change Management and Training:Successful implementation of AI requires effective change management and training for staff. Employees should be trained to understand AI tools, interpret AI-generated insights, and make data-driven decisions. Change management strategies should focus on fostering a culture of innovation and continuous improvement.
Challenges and Considerations
- Data Quality and Availability:The effectiveness of AI depends on the quality and availability of data. Incomplete, inconsistent, or inaccurate data can lead to incorrect predictions and suboptimal decisions. Ensuring high-quality data collection and addressing data gaps is crucial for successful AI implementation.
- Integration with Legacy Systems:Many manufacturing facilities operate with legacy systems that may not be compatible with modern AI technologies. Integrating AI with these systems can be challenging and may require significant upgrades or the development of custom interfaces.
- Security and Privacy:The use of AI in manufacturing involves handling sensitive data related to production processes and intellectual property. Ensuring data security and privacy is essential to protect against cyber threats and maintain competitive advantage.
- Scalability:Scaling AI solutions from pilot projects to full-scale implementation can be complex. Ensuring that AI systems can handle increased data volumes and maintain performance as they scale is critical for long-term success.
- Cost and ROI:Implementing AI involves significant upfront investment in technology, infrastructure, and training. Manufacturers need to carefully assess the potential return on investment (ROI) and develop a clear business case to justify the expenditure.
Future Directions
The future of AI in real-time production optimization looks promising, with continuous advancements in technology driving further improvements. Emerging trends such as edge computing, where data processing occurs close to the source, can reduce latency and enhance real-time decision-making. Additionally, the integration of AI with other technologies such as augmented reality (AR) and digital twins can provide immersive and interactive tools for monitoring and optimizing production processes.
Conclusion
Implementing AI for real-time production optimization represents a significant opportunity for manufacturers to enhance efficiency, reduce costs, and improve product quality. By leveraging advanced data analytics, machine learning, and real-time monitoring, AI can transform manufacturing operations and provide a competitive edge in the market. However, successful implementation requires careful planning, robust data infrastructure, continuous learning, and effective change management. As AI technology continues to evolve, its role in shaping the future of manufacturing will only grow, offering new possibilities for innovation and excellence.