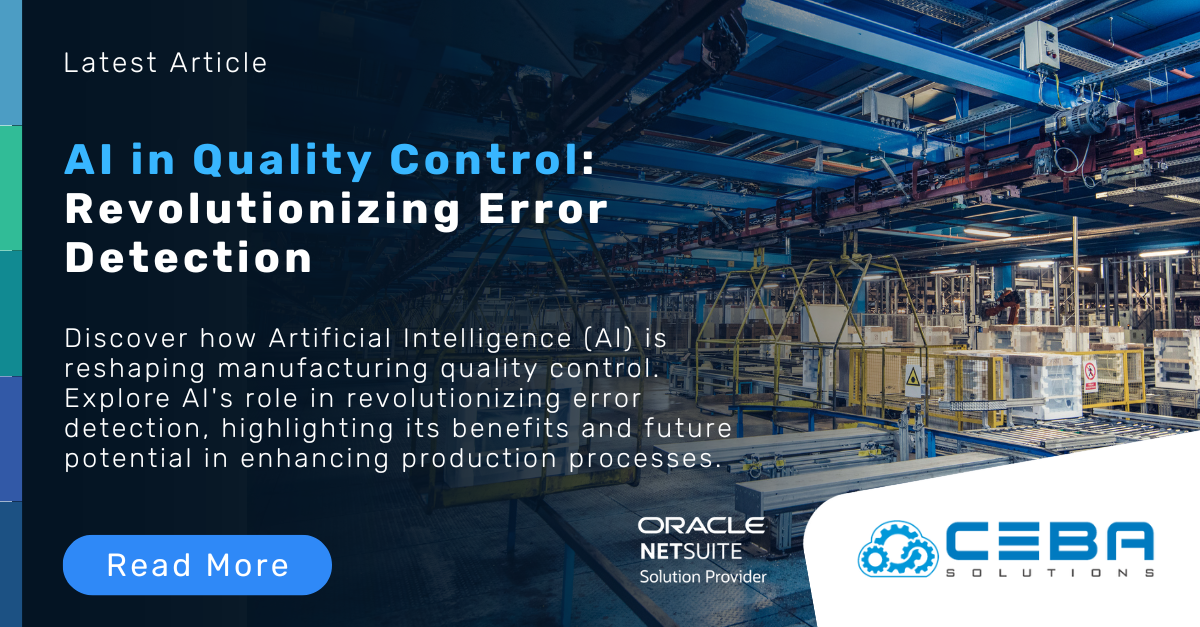
AI in Quality Control: Revolutionizing Error Detection
AI in Quality Control: Revolutionizing Error Detection
In the fast-paced world of manufacturing, ensuring the highest quality of products is paramount. Traditional quality control methods, which often rely on manual inspections and periodic sampling, can be time-consuming, error-prone, and inefficient. The advent of artificial intelligence (AI) is revolutionizing quality control by enabling more accurate, faster, and comprehensive error detection. This transformation is not only enhancing product quality but also boosting operational efficiency and reducing costs. This article explores how AI is revolutionizing error detection in quality control, the technologies involved, and the benefits and challenges of integrating AI into quality assurance processes.
The Evolution of Quality Control
Quality control has traditionally involved a combination of manual inspections and statistical sampling. Inspectors visually examine products, components, or processes for defects, while statistical methods help in identifying trends and predicting potential quality issues. While these methods have served industries well for decades, they are not without limitations. Human inspectors can miss defects due to fatigue or oversight, and sampling methods may fail to detect defects in unsampled batches.
The Role of AI in Quality Control
AI is transforming quality control by automating and enhancing the error detection process. Key technologies driving this transformation include machine learning, computer vision, and data analytics. Here’s how AI is being applied to quality control:
- Machine Learning:Machine learning algorithms analyze large datasets to identify patterns and anomalies that indicate defects. These algorithms can be trained on historical data to recognize different types of defects and predict potential quality issues. Over time, machine learning models improve their accuracy by learning from new data.
- Computer Vision:Computer vision systems use cameras and image processing algorithms to inspect products and components. These systems can detect visual defects such as cracks, scratches, misalignments, and discolorations with high precision. Advanced computer vision technologies, such as deep learning, enable the detection of complex defects that are difficult for human inspectors to identify.
- Real-Time Data Analytics:AI-powered quality control systems continuously monitor production processes in real-time. By analyzing data from sensors and IoT devices, these systems can detect deviations from normal operating conditions that may indicate quality issues. Real-time analytics enable immediate corrective actions, preventing defective products from reaching the market.
Benefits of AI in Quality Control
The integration of AI into quality control processes offers numerous benefits:
- Increased Accuracy:AI systems can detect defects with higher accuracy than human inspectors, reducing the likelihood of defective products reaching customers. This leads to improved product quality and customer satisfaction.
- Faster Inspections:AI-powered quality control systems can inspect products at high speeds, significantly faster than manual inspections. This reduces bottlenecks in production lines and increases overall throughput.
- Consistency and Reliability:Unlike human inspectors, AI systems do not suffer from fatigue or variability in performance. They provide consistent and reliable inspections around the clock, ensuring uniform quality standards.
- Cost Savings:By automating error detection and reducing the need for rework and recalls, AI-driven quality control can lead to significant cost savings. Additionally, early detection of defects helps in minimizing material waste and optimizing resource utilization.
- Enhanced Process Optimization:AI systems provide valuable insights into production processes, helping manufacturers identify and address root causes of defects. This continuous improvement cycle leads to better process optimization and higher overall efficiency.
Applications of AI in Quality Control
AI-driven quality control is being applied across various industries, each with its unique requirements and challenges:
- Automotive:In the automotive industry, AI is used to inspect parts and assemblies for defects such as surface flaws, weld integrity, and dimensional accuracy. AI systems ensure that vehicles meet stringent safety and quality standards.
- Electronics:The electronics industry leverages AI for inspecting printed circuit boards (PCBs), identifying soldering defects, component misplacements, and connectivity issues. High-precision inspections are critical for ensuring the reliability of electronic devices.
- Pharmaceuticals:In pharmaceutical manufacturing, AI systems inspect tablets, capsules, and packaging for defects. Ensuring the quality and integrity of pharmaceutical products is vital for patient safety and regulatory compliance.
- Food and Beverage:AI-driven quality control systems in the food and beverage industry inspect products for contaminants, packaging defects, and label accuracy. This helps in maintaining food safety and quality standards.
- Textiles:The textile industry uses AI to detect defects in fabrics, such as weaving faults, color variations, and tears. AI systems ensure that textiles meet quality standards before they are processed into finished products.
Challenges and Considerations
While AI offers significant advantages in quality control, its implementation is not without challenges:
- Data Quality and Availability:The effectiveness of AI systems depends on the quality and availability of data. Manufacturers need to ensure that data collected from production processes is accurate, complete, and relevant for training AI models.
- Integration with Existing Systems:Integrating AI-driven quality control systems with existing manufacturing infrastructure can be complex. Compatibility with legacy systems and seamless data flow between different platforms are essential for successful implementation.
- Initial Costs and ROI:Implementing AI systems involves initial costs for hardware, software, and training. Manufacturers must evaluate the potential return on investment (ROI) and ensure that the long-term benefits justify the expenditure.
- Skills and Expertise:Developing and maintaining AI-driven quality control systems require specialized skills in data science, machine learning, and engineering. Addressing the skills gap through training and hiring is crucial for successful deployment.
- Regulatory Compliance:In industries such as pharmaceuticals and automotive, regulatory compliance is critical. AI systems must adhere to industry standards and regulations to ensure that quality control processes meet legal and safety requirements.
Future Trends and Opportunities
The future of AI in quality control looks promising, with several emerging trends and opportunities:
- Edge Computing:Edge computing enables data processing at or near the source of data generation. This reduces latency and allows for real-time quality control in high-speed production environments.
- AI-Driven Automation:The integration of AI with robotic systems can automate not only error detection but also corrective actions. AI-driven robots can adjust production parameters, remove defective products, and perform rework autonomously.
- Predictive Quality Control:Combining AI with predictive analytics can help manufacturers anticipate quality issues before they occur. Predictive quality control uses historical data to identify patterns and trends that may lead to defects, enabling proactive measures.
- AI and Augmented Reality (AR):AR can enhance AI-driven quality control by providing real-time visual feedback to operators. AR interfaces can overlay inspection data on physical products, helping operators identify defects and take corrective actions.
Conclusion
AI is revolutionizing quality control in manufacturing by enabling more accurate, faster, and consistent error detection. By leveraging machine learning, computer vision, and real-time data analytics, AI-driven quality control systems enhance product quality, reduce costs, and improve operational efficiency. While challenges exist in terms of data quality, integration, and skills, the long-term benefits of AI in quality control make it a worthwhile investment. As technology continues to evolve, AI will play an increasingly vital role in ensuring the highest standards of quality in manufacturing, driving innovation and competitiveness in the industry.