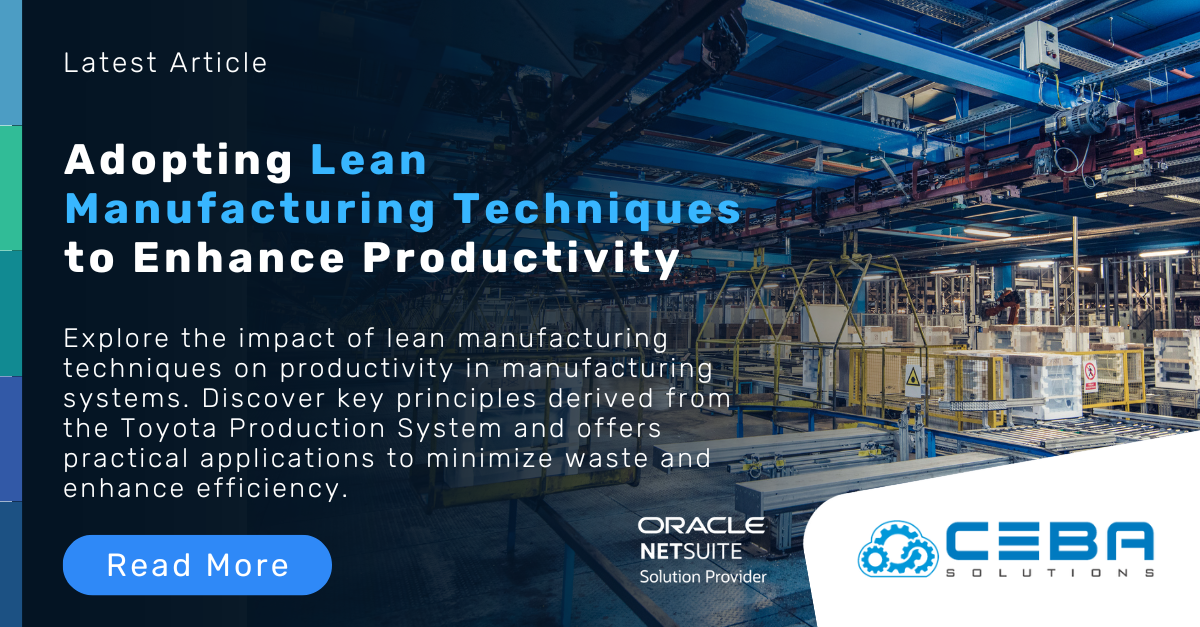
Adopting Lean Manufacturing Techniques to Enhance Productivity
Adopting Lean Manufacturing Techniques to Enhance Productivity
In the competitive landscape of modern manufacturing, businesses are constantly seeking ways to improve efficiency, reduce waste, and enhance productivity. Lean manufacturing, a methodology derived from the Toyota Production System, has proven to be a highly effective approach in achieving these goals. By focusing on value creation and waste elimination, lean manufacturing techniques enable organizations to streamline operations, improve quality, and respond more effectively to customer demands. This article explores the principles of lean manufacturing, its core techniques, and the benefits it brings to enhancing productivity.
Principles of Lean Manufacturing
Lean manufacturing is built on five fundamental principles that guide its implementation:
- Value: Identify what value means from the customer’s perspective and focus on delivering it. This involves understanding customer needs and ensuring that all activities contribute to creating value for the customer.
- Value Stream: Map the entire value stream, which includes all the steps and processes involved in delivering the product or service. Identify and eliminate non-value-adding activities, also known as waste.
- Flow: Ensure that the value-creating steps flow smoothly without interruptions. This involves optimizing the workflow to minimize delays and bottlenecks, ensuring a continuous and efficient production process.
- Pull: Implement a pull-based system where production is driven by actual customer demand rather than forecasted demand. This reduces overproduction and inventory costs, aligning production more closely with customer requirements.
- Perfection: Continuously strive for perfection by seeking to improve processes and eliminate waste. This principle emphasizes the importance of ongoing improvement and the involvement of all employees in the pursuit of excellence.
Core Lean Manufacturing Techniques
Several key techniques are central to the successful implementation of lean manufacturing:
- 5S Methodology:The 5S methodology is a systematic approach to workplace organization, aiming to improve efficiency and safety. The five steps are:
- Sort (Seiri): Remove unnecessary items from the workspace.
- Set in Order (Seiton): Arrange necessary items for easy access.
- Shine (Seiso): Keep the workspace clean and tidy.
- Standardize (Seiketsu): Establish standards for maintaining organization and cleanliness.
- Sustain (Shitsuke): Continuously uphold and improve the 5S practices.
- Kaizen (Continuous Improvement):Kaizen involves small, incremental improvements made regularly to enhance processes and reduce waste. It encourages employee participation and fosters a culture of continuous improvement.
- Value Stream Mapping (VSM):Value stream mapping is a visual tool used to analyze and optimize the flow of materials and information required to deliver a product or service. VSM helps identify inefficiencies and areas for improvement.
- Just-In-Time (JIT):Just-in-time is a production strategy that aims to produce and deliver products in the exact quantities and at the precise time they are needed. JIT reduces inventory costs and minimizes waste from overproduction.
- Kanban:Kanban is a visual scheduling system that helps manage workflow and inventory. It uses cards or signals to indicate when new materials or components are needed, ensuring a smooth and continuous production flow.
- Total Productive Maintenance (TPM):TPM focuses on maintaining and improving equipment to prevent breakdowns and ensure optimal performance. It involves regular maintenance, employee training, and proactive measures to extend equipment life and reduce downtime.
- Six Sigma:While Six Sigma is often considered a separate methodology, it complements lean manufacturing by focusing on reducing process variation and improving quality. Six Sigma uses statistical tools and techniques to identify and eliminate defects and improve process performance.
Benefits of Lean Manufacturing
Adopting lean manufacturing techniques brings numerous benefits that enhance productivity and overall business performance:
- Increased Efficiency:Lean manufacturing eliminates waste and optimizes processes, resulting in increased operational efficiency. This leads to faster production cycles, reduced lead times, and higher output.
- Improved Quality:By focusing on value creation and continuous improvement, lean manufacturing enhances product quality. Reducing defects and errors leads to higher customer satisfaction and fewer returns or recalls.
- Cost Savings:Lean techniques reduce waste in various forms, including excess inventory, overproduction, and unnecessary transportation. These reductions translate to significant cost savings, improving the company’s bottom line.
- Enhanced Flexibility:Lean manufacturing enables organizations to respond more quickly and effectively to changes in customer demand. A pull-based system and optimized workflows allow for greater flexibility and adaptability.
- Employee Engagement:Lean manufacturing promotes a culture of continuous improvement and empowers employees to contribute to problem-solving and process enhancements. This leads to higher employee engagement, job satisfaction, and retention.
- Sustainability:By minimizing waste and optimizing resource use, lean manufacturing supports sustainable practices. Reducing the environmental impact of production processes aligns with corporate social responsibility goals and can improve the company’s reputation.
Implementing Lean Manufacturing
Implementing lean manufacturing requires a strategic approach and commitment from all levels of the organization. Here are key steps to successfully adopt lean techniques:
- Leadership Commitment:Strong leadership commitment is essential for driving lean initiatives. Leaders must set clear goals, allocate resources, and foster a culture that embraces lean principles.
- Employee Involvement:Engage employees at all levels in the lean transformation process. Provide training and encourage participation in identifying and implementing improvements. Employee buy-in is critical for sustainable success.
- Assessment and Planning:Conduct a thorough assessment of current processes and identify areas for improvement. Develop a detailed plan for implementing lean techniques, including timelines, milestones, and performance metrics.
- Pilot Projects:Start with pilot projects to test lean techniques and demonstrate their benefits. Successful pilot projects can serve as models for broader implementation across the organization.
- Continuous Improvement:Lean manufacturing is an ongoing journey rather than a one-time initiative. Continuously monitor performance, seek feedback, and make adjustments to drive further improvements.
Conclusion
Adopting lean manufacturing techniques is a proven strategy for enhancing productivity, improving quality, and reducing costs. By focusing on value creation, waste elimination, and continuous improvement, lean manufacturing transforms operations and positions organizations for long-term success. As manufacturers navigate the challenges of a competitive global market, embracing lean principles offers a path to greater efficiency, flexibility, and sustainability. By committing to lean manufacturing, businesses can unlock new levels of performance and achieve a competitive edge in their industry.